Minimise sinter degradation between sinter plant and blast furnace exploiting embedded real-time analytics (MinSiDeg) project abstract
Sinter with high and consistent quality, produced with low costs and emissions is very important for iron production. Transport and storage degrade sinter quality, generating fines and segregation effects.
Conventional sinter quality monitoring is insufficient: Slow and expensive. Consequently, the impact of sinter quality on daily BF operation is extremely intransparent.
In MinSiDeg, new transfer systems and procedures will minimise degradation during transfer to save return fines and stabilise particle size distribution.
New on-line measurements will be established, combined and exploited with Big Data technologies. This break-through in continuous quality monitoring will enable combined optimisation of sinter plant and blast furnace.
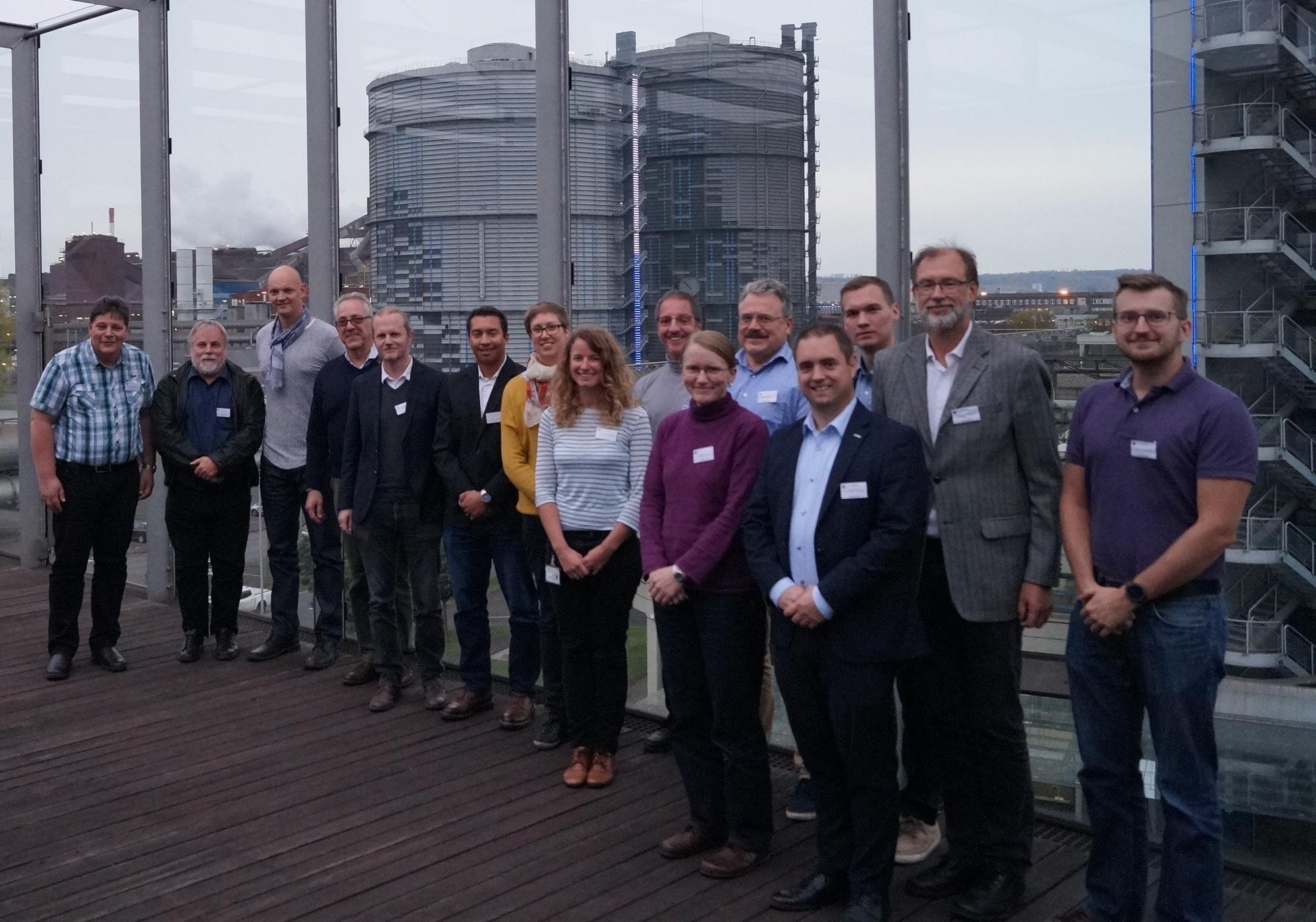
Kick-off-Meeting for „Minimise sinter degradation between sinter plant and blast furnace exploiting embedded real-time analytics“ (MinSiDeg) in Linz
MinSiDeg objectives
Major objective of the project MinSiDeg is to clearly decrease costs and environmental impact of sinter plants and blast furnaces. To achieve this, the sinter quality will be optimised along the production chain improving both, sinter plant and blast furnace working.
The following general technical objectives are defined:
- quantify sinter quality fluctuations (minutes to several hours)
- intensify the exploitation of data by Big Data methods
- minimise sinter degradation by material handling
- make (physical) sinter quality transparent and more stable
- improve BF shaft permeability
MinSiDeg will realise the objectives by 3 main approaches (cf. Figure 1):
- Online monitoring of physical sinter quality by new measurements
- New equipment and material handling procedures along the transfer to the blast furnace
- Real-time analytics of existing and new data streams for machine supported decisions
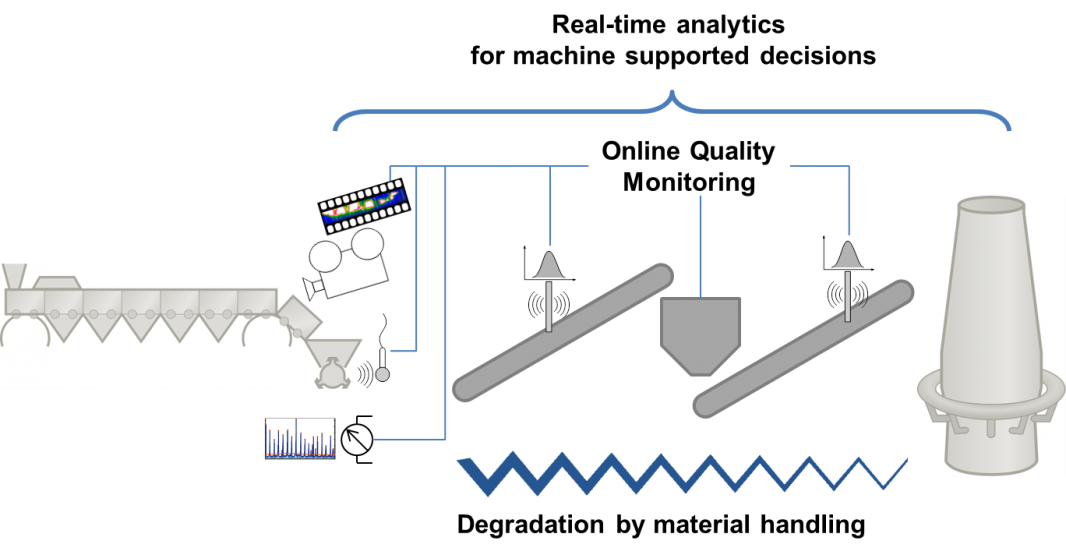
Figure 1: Main approaches within the MinSiDeg concept.
MinSiDeg research approach
The project work will be organised within 5 technical work packages:
- Improve sinter stability
- Minimise sinter degradation along transport and storage
- New online methods for sinter quality determination
- Improve value of sinter for the blast furnace
- Real-time machine supported decisions on sinter quality
The involved partners in this research project are
VDEh-Betriebsforschungsinstitut GmbH |
 |
thyssenkrupp Steel Europe AG |
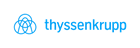 |
voestalpine Stahl GmbH |
 |
DK Recycling und Roheisen GmbH |
 |
K1-MET GmbH |
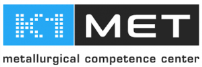 |
Montanuniversität Leoben |
 |
The project leading to this application has received funding from the Research Fund for Coal and Steel under grant agreement No. 847334. |
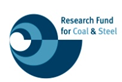 |
Project duration: 1 July 2019 – 31 December 2022 (42 months)