REUSteel
Dissemination of results of the European projects dealing with reuse and recycling of by-products in the steel sector
REUSteel project abstract
European Research dedicated a lot of time and efforts in the development of innovative sustainable solutions for the steel industry. The aim is to provide bridging solutions to lead the steel industry towards a reduction of its environmental impact with an obvious saving of natural resources, hence in being closer to a virtuous objective of “zero waste” goal. These thematic fields are perfectly framed in a concept that is strongly emphasized at a European level and that is receiving increasing attention in the scientific and technical community in the latest years, namely the so called Circular Economy. The circularity concept pushes researchers and industries to look for synergies with other industrial sectors to analyze and investigate solution for improving by-product reuse and recycling both inside and outside the steelmaking cycle, by thus developing examples of industrial symbiosis. However, the joint efforts of the EU steel industries on this theme are still not widely known.
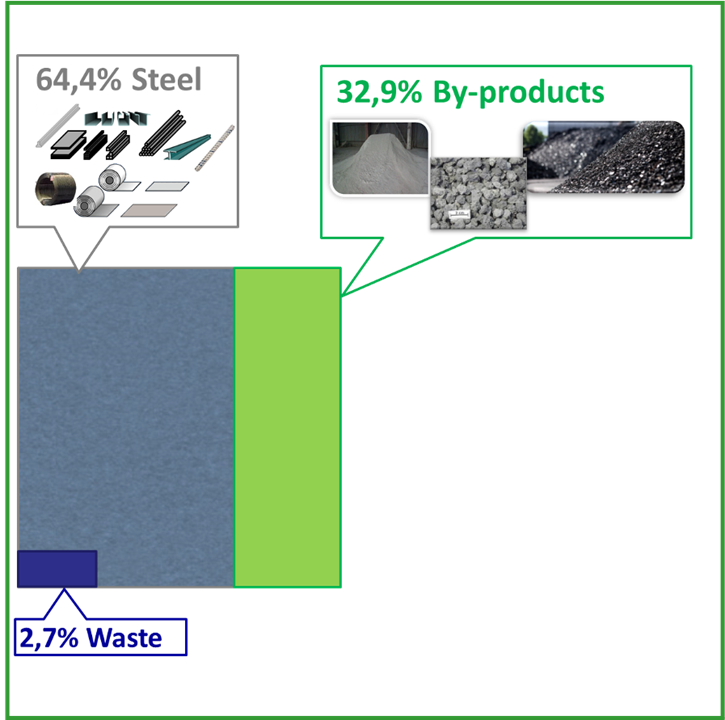
REUSteel project aims at extensively disseminating and valorizing important research results on the reuse and recycling of byproducts, based on an integrated critical analysis of many list of EU-funded projects, in order to promote the results exploitation and increase the synergies with other sectors.
REUSteel project overview
“Dissemination of results of the European projects dealing with reuse and recycling of by-products steel sector (REUSteel)” is a project co-founded by the Research Fund for Coal and Steel (RFCS).
The project is framed in the context of more eco-friendly and sustainable solutions in the steel industry. The reuse and recycling of by-products of the steelmaking cycles as well as on the exploitation of by-products from other activities outside the steel production cycle, such as alternative carbon sources (e.g., biomasses and plastics) are the proper actions to move towards a saving of the natural resources together with a reduction of the environmental impact, hence being closer to a “zero-waste” goal.
“REUSteel” aims at an extensive action of dissemination and valorisation of the most important research results on by-products reuse and recycling, based on an integrated critical analysis of many EU-funded projects, in order to promote results exploitation and increase the synergies with other industrial sectors. This analysis will allow identifying the most urgent needs and ambitions of the European steel sector and defining a sequence of future research topics in this field.
A joint critical analysis, carried out by all the partners, belonging to different institutions, will provide new insights and guidelines for future research topics in this field, in order to promote the dissemination and, consequently, the implementation of the achieved results. The project will also organise the results, in order to present selected groups of topics at planned workshops and seminars. This will provide a clearer vision of the outcomes to stakeholders and new audiences, in order to get new and deeper indications for a new roadmap, future synergies with other sectors and industrial trends.
“REUSteel” will contribute to an update of the steel roadmap for a low carbon Europe 2050 and the current BIG-Scale initiative of EUROFER.
The involved Partners in the research project are:
The Project Coordinator is Dr. Eng. Valentina Colla (valentina.colla@santannapisa.it)
REUSteel dissemination action
The project was finalized in January 2022. Further information about events, videos and public deliverables as the roadmap of the REUSteel project can be found on https://www.reusteel.eu/index.html
- Events:
https://www.reusteel.eu/events.html
- Documents and Videos
https://www.reusteel.eu/documents.html
- Public Deliverables
https://www.reusteel.eu/deliverables.html
This project is carried out with the financial support of the Research Fund for Coal & Steel – Grant Agreement Number: 839227 (2019)